Process Improvement
Description
Utilizing a strengths-based approach to align your “how” to your “why”.
Services and Specialties
Gardening Analogy
Making sure your tools (seeds, shovels, fertilizer, stakes, hose, planting/watering schedule, etc) are available, organized, and utilized effectively to grow what you value.
Systems
Change
Description
Understanding and improving the systems that shape our communities through collaboration grounded in shared values.
Services and Specialties
Gardening Analogy
Learning about the ecology of your area (climate, soil, water, pollinators, animals) to understand how it impacts your garden and how you can set yourself up for success while protecting and improving the ecosystem.
People Development
Description
Empowering personal and organizational growth through coaching, training, and culture-building.
Services and Specialties
Gardening Analogy
Investing in your team’s capacity to grow your shared garden successfully and sustainably through education, recognition, and creating a culture of belonging.
Cultivating Growth’s specialized Approaches
Community-Based System Dynamics (CBSD)
System Dynamics is a methodology that was created by engineers in the 1950s to better understand industrial production systems. Over time, it has grown and evolved to be used in many contexts, including social work, public health, and public policy.
Cultivating Growth specializes in a subset of System Dynamics called Community-Based System Dynamics: “Community-based system dynamics (CBSD) is a participatory method for involving communities in the process of understanding and changing systems from the endogenous or feedback perspective of system dynamics” (p.1)1.
We work collaboratively with our partners to define the problem they’re facing and then design workshops with staff, community members, and other stakeholders. In these workshops we guide participants through activities that unearth each person’s mental models of the problem and then create a shared visual model of the system that underlies the problem. We can then understand how that system operates and changes over time and what factors and feedback loops influence the behavior they observe in real life. We can also identify leverage points where they can effectively and efficiently intervene to change how the system behaves according to their goals.
This approach is adaptable to each partner and each project. From the number and content of the workshops, to the deliverables, to the accommodations to support full, authentic participation, every aspect of the process is designed collaboratively to make sure it works well for the partner and those involved in the process. Throughout our collaboration, we make sure we’re training our partners in the methodology so that they can continue to use it to support their work, with or without Cultivating Growth.
- Hovmand, P. S. (2014) Community-Based System Dynamics. Springer Science+Business Media. ↩︎
The main goal [of System Dynamics] is to help people make better decisions when confronted with complex, dynamic systems.
System Dynamics Society – “What is System Dynamics?”
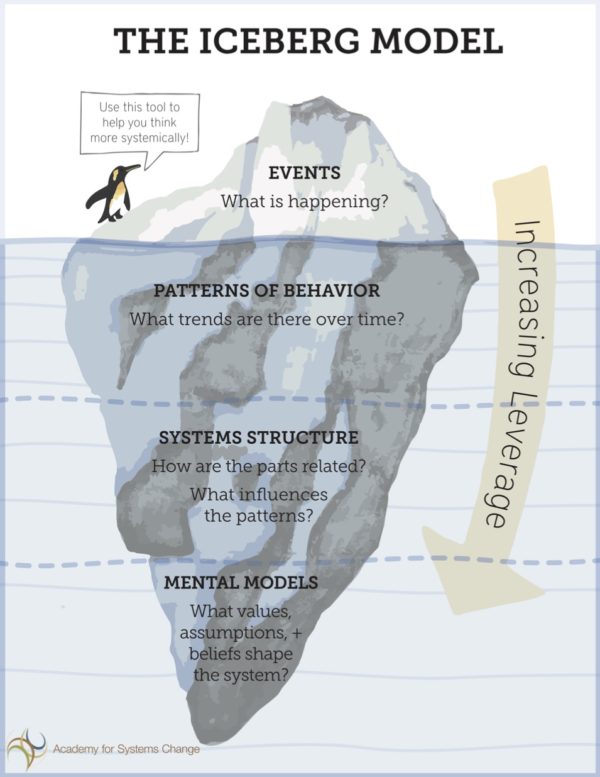
Lean and the improvement Kata
Lean is a philosophy and methodology that originated with Toyota in Japan and is most commonly found in manufacturing and production industries around the world. Its focus is on continuous process improvement and reducing “waste” in production. In this context, “waste” refers to any part of the manufacturing process that does not add value to the end product. It’s not just about what goes in the dumpster – it’s also about wasted time, wasted energy, wasted resources, and wasted talent. The goal is to equip your organization and your team to identify waste in all its forms, propose and test ways to reduce that waste, and continuously improve so you waste less and spend more time on what matters most.
While it originated in manufacturing, the value of the Lean philosophy and practices extend beyond just that industry. For example, it is being used increasingly in health care and other sectors where efficiency and continuous improvement are valuable. At Cultivating Growth, we believe that the philosophy, principles, and practices of Lean can help the social sector, including non-profits, make better use of precious resources and innovate to the benefit of our organizations and communities. Lean isn’t just about increasing efficiency for profit’s sake alone. At its core, Lean must be grounded in a clear purpose and investment in learning and community, all of which can apply in any sector.
“Building a learning community means having individuals with the capacity to learn. This is the basic starting point. Beyond this, a community suggests belonging, and individuals cannot belong if they are short-term labor to be fired at will as soon as there is an economic downturn. Belonging to a community suggests reciprocity: a commitment by the individual to the community, and a commitment by the community to the individual.“
Liker, J. (2006) The Toyota Way Fieldbook: A Practical Guide for Implementing Toyota’s 4Ps, p.21
Cultivating Growth applies this core philosophy of Lean along with tools of continuous improvement in its Process Improvement services. Once we understand your purpose, we look at your community, team, and processes. Then, together, we identify where you may be wasting precious resources and take intentional, data-driven steps to improve, always grounded in your purpose.
To foster a culture of continuous improvement in your organization, Cultivating Growth can set you up to follow what Mike Rother described as The Improvement Kata and Coaching Kata, based on his observations of how Toyota learns and improves.
“A kata typically refers to fundamental movements in Japanese martial arts, but can refer to any basic form, routine, or pattern of behavior. Recognizable patterns of behavior and clear expectations make it easy to recognize abnormalities (problems) and also serve as a basis of improvement, setting and attaining higher standards.
https://www.lean.org/lexicon-terms/kata/
In lean management, kata refers to two linked behaviors: improvement kata and coaching kata…[which are] an effective way to develop the scientific problem-solving method of PDCA [plan, do, check, act] and embed it in an organization’s work processes.“